Kamikoto’s 19-Step Practice
Each Kamikoto knife goes through a rigorous 19-step process that takes several years from start to finish to complete. With more than 100 years of experience between them, our expert bladesmiths forge and shape raw steel into hardy blades, polishing and sharpening them to an excruciatingly fine edge. Each blade is individually inspected before it leaves the forge, ensuring that every single Kamikoto knife stays true to the Japanese legacy of crafting single-bevel Japanese steel knives of an exceptional quality. Kamikoto knives are a study in skill; you feel the spirit of the craft in every piece.
Fully versed in traditional blade-making practices, Kamikoto's blades are handmade by a select group of experienced craftsmen in Niigata, Japan, where blacksmithing can be traced back to before the Edo period, as well as in Yanjiang, China – a town with over 1,000 years of knife and sword making heritage. Today, Yanjiang is the leading center of Japanese-style knife forging, polishing and balancing – where the Japanese legacy is preserved, and carried on, with reverence for the skill of the knifesmiths who evolved this craft centuries ago.
A Legacy of Excellence
Kamikoto appreciates that a good product is incomplete without great service. Our work does not end with the craftsmanship of a flawless blade. Understanding and anticipating a client's needs is integral to the Japanese spirit of omotenashi, or the philosophy of selfless hospitality. Kamikoto's goal is to respond to clients' needs clearly and quickly, delivering the same high quality in Kamikoto 神箏 service as is found in Kamikoto 神箏 products; and to strive to see things from our client's perspective as well as from our own.
Kazuomi Yamamoto
Fourth-Generation Master Knifesmith
Chairman, Kamikoto 神箏 Advisory Board
Yamamoto-san is a fourth-generation master knifesmith and Chairman of the Kamikoto 神箏 Advisory Board. He continues to work in the company founded by his great-great grandfather in 1908. A family of swordsmiths, Yamamoto-san’s ancestors made their living forging traditional katana blades. The family refined steel and made katana blades for the Japanese Navy. Yamamoto-san sees the knife industry in Niigata as one born of necessity and demand, and is optimistic that this ancient craft will stay alive and flourish for many generations to come.
Tsuyoshi Inagaki
Client Relationship Manager
Client Relationship Manager Inagaki-san is the primary point of contact for Kamikoto 神箏 clients in Tokyo. Inagaki-san endeavors to embody the Kamikoto 神箏 philosophy to deliver an exceptional product, and to think and act from the client’s viewpoint. Inagaki-san is a knowledgeable blade and culinary expert and is always ready to share his honing and sharpening skills with clients who require assistance with keeping their Kamikoto 神箏 knives in pristine shape.
“While the world around us has moved to less exacting production techniques, Kamikoto 神箏 has stayed true to its original values based on craftsmanship and quality
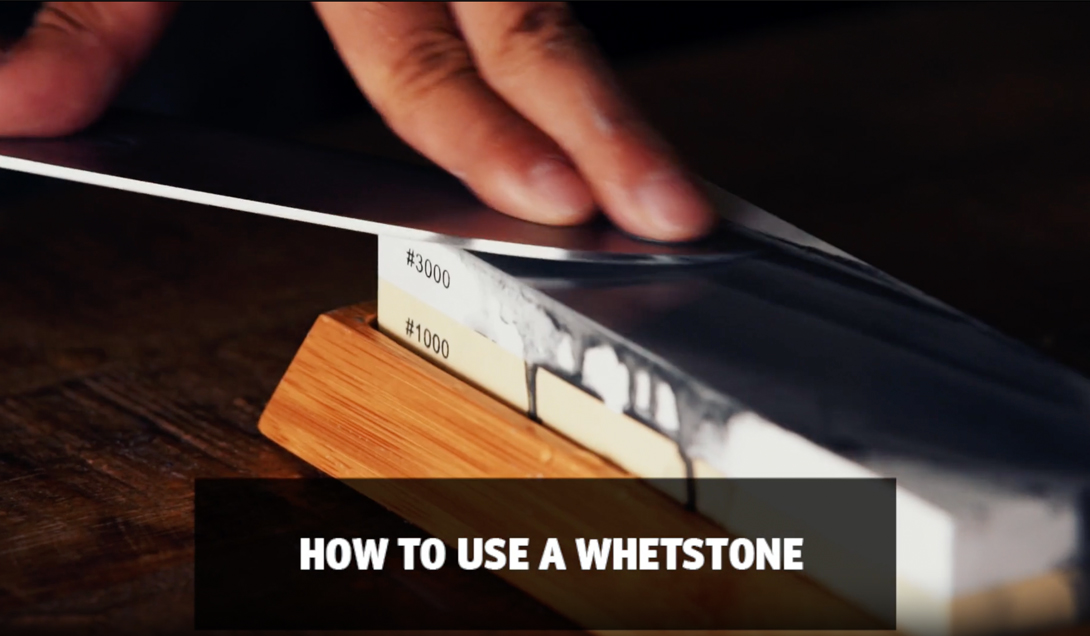